"A modern composite with a sober, refined elegance"
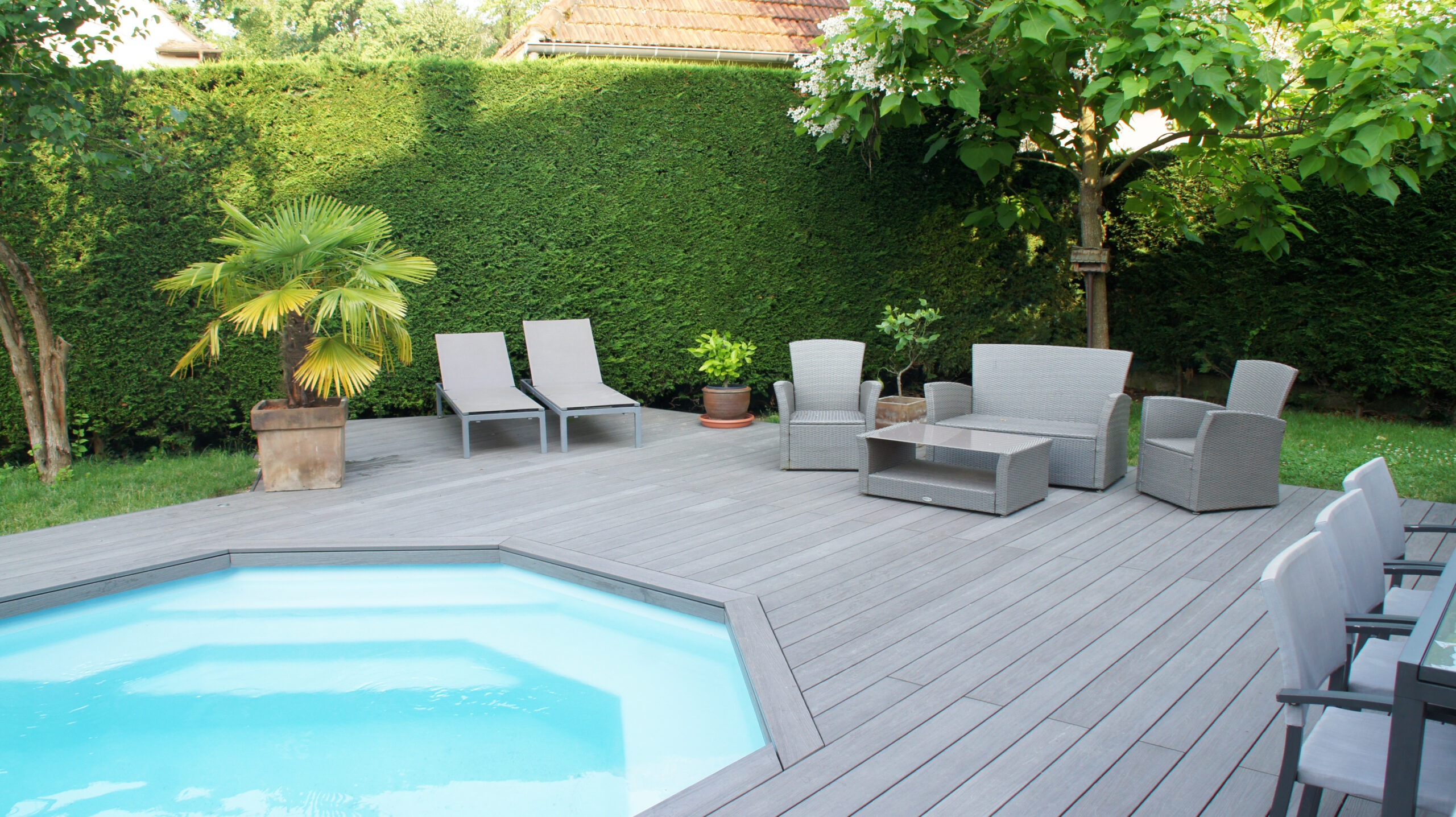
A perfect blend of modernity and durability
- Elegant grey colour, ideal for contemporary projects
- Matt finish and subtle veining for an authentic, natural look
- Co-extruded composite for durability and strength, without compromising aesthetics
- Resistant to stains, slipping and extreme weather conditions
- Ideal for modern outdoor design, combining performance, style and ease of maintenance.
Wood ageing
Nekko, whether brown or grey, ages with great stability thanks to its co-extruded composite design. Unlike natural wood, it greys very little, if at all, over time and retains its original colour for a long time. Its protective outer layer makes it UV, weather and stain resistant, preventing any discolouration or major changes to its appearance. Minimal maintenance is required to maintain its aesthetic appearance.
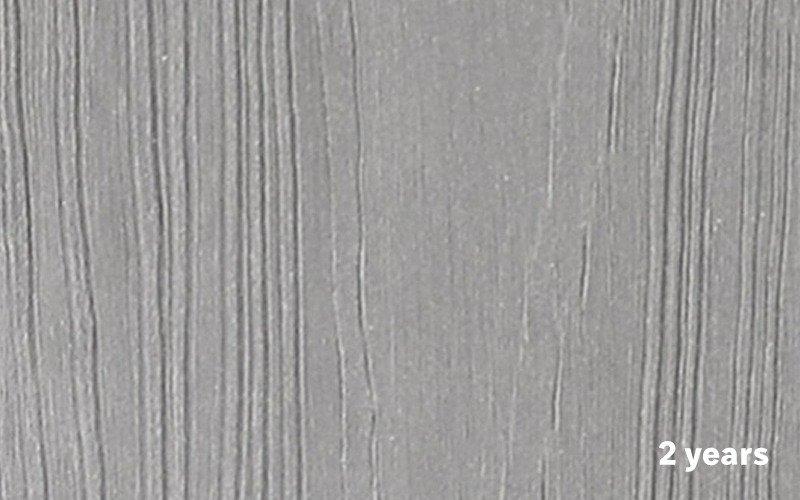
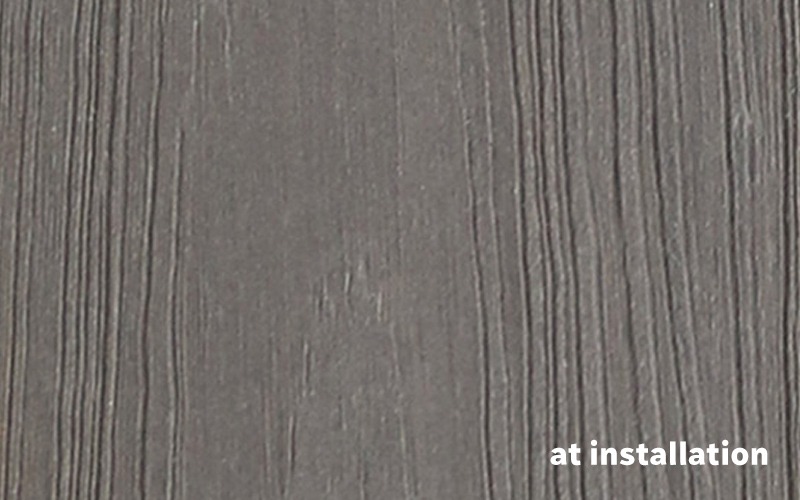
A modern, high-performance composite
Nekko Grey, designed in co-extruded composite, combines wood fibres and high-density polyethylene to create a durable, hard-wearing material, that meets the highest standards for outdoor landscaping.
Protection and durability
Its advanced protective coating ensures optimum resistance to UV rays, moisture, stains and climatic variations , guaranteeing a reliable, easy-to-maintain product, even in demanding conditions.
Contemporary and enduring elegance
With its modern grey colour and slightly textured matt finish, Nekko Gris retains its original colour over time, adding a refined, sober touch to your contemporary outdoor design projects.
Treatment process
Nekko is a co-extruded composite material made from a blend of wood fibres and high-density polyethylene (HDPE), reinforced with additives. This process combines the advantages of wood and plastic, offering both natural aesthetics and enhanced durability.
Preparation of the raw materials:
Wood fibres (approximately 55% for the core) are mixed with high density high-density polyethylene (HDPE) and specific additives (UV stabilisers, colour pigments, binding agents), colour pigments, binding agents ).
Core extrusion:
The mixture is heated and extruded to form the core of the blades, guaranteeing a stable and homogeneous structure.
Co-extrusion of the protective layer:
A thin outer layer (approximately 45% wood and 40% HDPE ) is co-extruded onto the surface. This protective coating enhances resistance to stains, scratches, UV and weathering.
Cooling and finishing:
Extruded planks are cooled and calibrated to the desired dimensions. A brushed or matt finish is added for a pleasing look and feel.
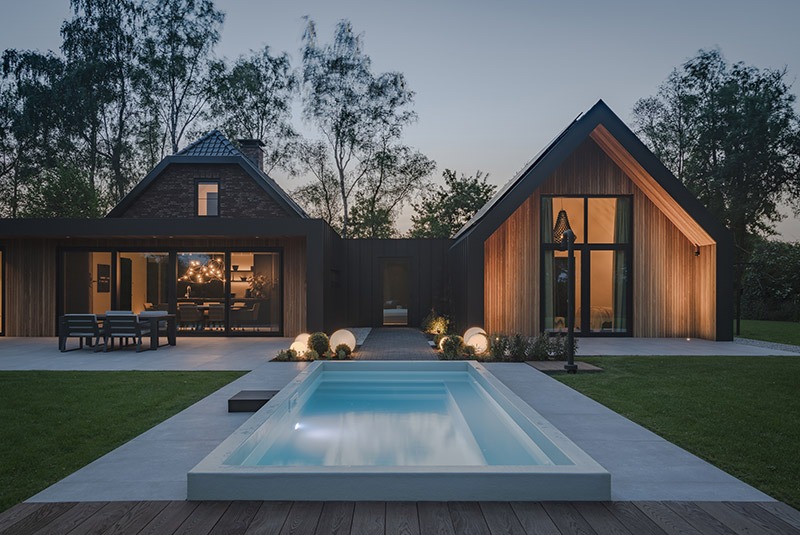
Applying Kebony®
Kebony uses a patented modification process called furfurylation.
Furfurylation uses a biological liquid called furfuryl alcohol, derived from agricultural plant waste. Furfuryl alcohol is injected into the sapwood cells and, when combined with heat, bonds permanently, transforming softwood into hardwood. Although chemicals are used, the product is non-toxic, both during and after service.
Lorem ipsum dolor sit amet consectetur adipiscing elit dolor
Lorem ipsum dolor sit amet consectetur adipiscing elit dolor
Lorem ipsum dolor sit amet consectetur adipiscing elit dolor
Case studies
Our deck boards are certified
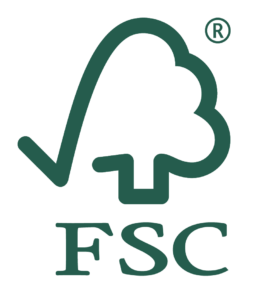
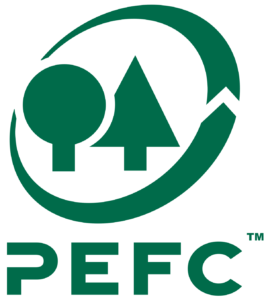